
Author: Ben Hartman | July 17, 2025 | 6 Min Read
Key Steps to Streamline Employee Training and Improve Safety Culture in Food

A strong safety culture is essential for risk management and recall prevention, and also helps companies meet the compliance demands of the food industry. But building this culture amid the daily demands of food manufacturing can be challenging.
At Rootwurks, we surveyed almost 200 food industry professionals - from front-line workers to executives - for a report on the biggest training challenge they face when building safety culture.
The top challenge mentioned in our report, “The Biggest Training Challenges in the Food Manufacturing Industry,” was “lack of time.” But a wide range of hurdles were mentioned, including workforce engagement, knowledge retention, and lack of leadership buy-in.
After publishing the report, we interviewed Harmeet Kaur, Director of Training and Consulting Services for ASI Food Safety, to get her assessment of what companies can do to make training more efficient and effective and to build a more formidable safety culture.
Management Must Commit to Safety Training
Kaur said that the first step in building a more efficient, effective food safety program is to get management on board.
“The majority of the complaints that we receive in my classes are that the management is not committed to food safety. I would say start with management commitment because your food safety manager and QA (quality assurance staff) aren't going to take on the burden alone.”
She said that management must “lay out the mission and vision of the company,” adding that to streamline operations, “the best thing to do is to engage management and have them understand what they need to do and then invest in your food safety culture.”
In our latest report, “lack of leadership buy-in” was mentioned as the top training challenge by 4.9% of all respondents. But this figure changed according to the respondent's job title or the size of the company they work for. For instance, among senior leadership, 10.7% cited lack of leadership buy-in, though among frontline employees, it was not among the top 5 challenges mentioned. It was cited by 28.6% of respondents from companies with 1,000 to 5,000 employees, and by 20% at companies with more than 5,000 employees. It was not mentioned as a top challenge at smaller companies with 0-500 employees.
“An area where food safety in general struggles a lot is when there’s no management commitment, they don't want to do internal audits, they don't want to support employees.”
Kaur said that management must understand that there is a clear return on investment for quality assurance and food safety, in that they are central to everything the company is trying to do.
“Without quality assurance and food safety, you cannot ship the product; there's such a huge liability right there. So the first thing to do is to engage management so they understand why we need to do this and provide the resources for food and QA.”
Empower Employees, Build Safety Culture, Save Time
In late June, Kaur led an ASI webinar entitled “Empowering Employees to Lead in Food Safety: Building a Collaborative Culture.”
In the webinar, she focused on several key topics in employee empowerment and team collaboration, including how to foster shared ownership, build cross-functional collaboration, communication strategies, training, and engagement, and real-world applications of these best practices.
Kaur mentioned shared ownership and communication repeatedly in her chat with Rootwurks, and the importance of encouraging frontline employees to have a voice on food safety.
“When you engage and empower employees and give them the tools and resources they need, they can problem solve and will have decision-making power.”
She said this streamlines operations because decisions can be made with confidence by employees on the floor without having to go up the chain of command and wait to be told what to do.
“Safety culture is what we do when no one is watching. You need to empower employees to make decisions on the floor without looking for management.”
Kaur said that employees need the training to take the lead on the floor and also know that they can speak up about safety issues without fear of retaliation.
Encourage and Praise Employees
Kaur said that companies should avoid a “fear-based culture” and instead one in which management makes a point of addressing employees on a one-on-one basis when they have performed their jobs well, and not only when they fall short of expectations.
“It’s about just going onto the floor and saying that someone did a good job…Sometimes management fails to notice what small gestures do.”
She added, “I’ve worked at a really good company where management goes on the floor and will say good things to the employees who were so happy to see people on the VP level or senior level that don’t show up on the floor much. I think making appearances on the floor makes a difference, much more than sitting in a fancy office.”
She stated that a positive workplace environment fosters improvement and more effective operations and is part of an “open-door culture” in which employees know that they can come and speak to management and make suggestions without fear of retaliation.
Save Time with Custom Training
Kaur also highlighted “task-based, customized training” that answers a facility's unique needs as a way to save time on training.
“Hazards are different, and in order to engage more people, you need to get more realistic about their jobs and what they face.”
She spoke of the importance of training that “can be customized based on your operations,” rather than one-size-fits-all learning, using the example of an instructor trying to teach employees on the guidelines for processing blueberries, even though they work at a dairy company.
“Your hazards are different, so to engage more people, you need to be more realistic about their job and your operations and what kind of problems you face, and that’s how you come up with solutions.”
She used the example of sanitation, saying that many people receive non-conformities for sanitation because it's a task that can have very specific formulations for the types of chemicals and equipment used, and shouldn’t be done in a generalized, one-size-fits-all fashion.
Continuous Improvement is Key to Safety
To get the most out of your food safety program, training must focus on continuous improvement for employees, rather than just doing the minimum.
“Continuous improvement should be the tagline, instead of just doing the minimum to get the passing grade, or pass the audit and then be done with it.”
Kaur said that internal audits are one of the best ways to learn how to foster improvement in operations.
“The idea of internal audits is not to just find the gap and do the corrective action, but also to learn how we can improve our system so when we get a non-conformance, even if it is a small one on a SOP, we can fix it as part of a continuous improvement.”
Continuous improvement can also be seen in simple time-saving measures like making SOPs more concise and clear so that they can be readily followed and understood, without taking as much time out of the workday.
It can also mean hiring bilingual employees in order to improve your ability to communicate with your team members and remove the slowdowns brought on by the language barrier.
But much like she mentioned earlier in the interview, it's also about having an approach that doesn’t focus on the blame game.
“Continuous improvement means the mindset should be not to blame employees or management [when things go wrong] but to think about how we are improving our systems and our work culture so we can do better.”
Rootwurks Training: Cut Downtime without Cutting Corners
At Rootwurks, we’ve developed a fully customizable food safety training and compliance adherence platform that helps companies build more streamlined, targeted training for food safety and risk management. To learn more about our solutions, reach out to the Rootwurks team here:
Contributors
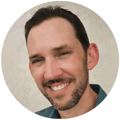
Ben Hartman
From HACCP certification to the basics of hygiene, our on-demand courseware has you covered.
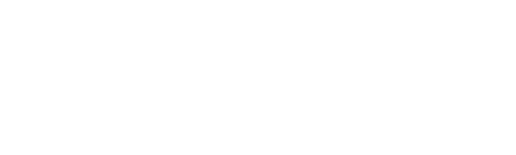