
Author: Ben Hartman | March 21, 2024 | 4 Min Read
Kroger Traceability Program to Go Well Beyond FDA Requirements
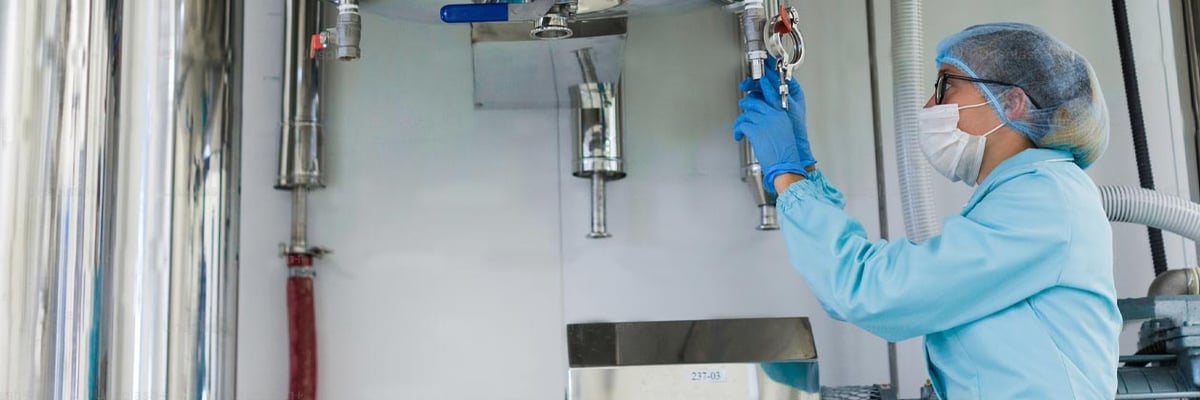
The Kroger Company will implement a traceability program that goes far beyond the FSMA 204D requirements of the Food and Drug Administration, Food Safety Magazine reported.
In December 2023 The Kroger Co published a food traceability policy and requirements document to guide suppliers on the new system. The document states that “Kroger intends to collect and record traceability information for all food products entering Kroger facilities, to ensure the safety of food supply for every customer.”
The Kroger document also states that suppliers must adhere to the guidelines in Kroger’s EDI 856 ASN (Advance Shipping Notice), provide an EDI 856 ASN document for every shipment to any Kroger facility, align logistical unit requirements to Kroger’s supply chain receiving specifications, and certify that palletized barcode labels on physical products arriving at the receiving dock correspond to the EDI 856 ASN data transmission.
FSMA 204D: What Does it Cover?
By January 2026, all food industry companies operating in the U.S. that manufacture, process, pack, or hold foods on the FDA’s Food Traceability List must implement the specific recordkeeping requirements detailed in Section 204D of the FDA Food Safety Modernization Act (FSMA).
The food traceability list includes certain cheese products, shell eggs, nut butters, crustaceans, molluscan shellfish, bivalves, ready-to-eat deli salads, fresh-cut leafy greens, finfish (fresh, frozen, and smoked), and fresh cucumbers, herbs, leafy greens, melons, peppers, sprouts, tomatoes, tropical tree fruits, and vegetables.
Under FSMA 204D, companies that manufacture, process, or pack foods on the traceability list must maintain records containing Key Data Elements associated with specific Critical Tracking Events (CTEs) and be able to provide information on a spreadsheet to the FDA within 24 hours if requested.
The FDA does not require that companies use a specific application or technology to perform recordkeeping of these processes. The FDA writes that records may be kept on paper, but that the FDA may in cases of a threat to public health request that information about specific foods be provided on an electronic sortable spreadsheet.
The Kroger Co takes the requirements further and applies them to all food products entering company facilities. In addition, Kroger is requiring all suppliers to adhere to these steps by June 20, 2025, six months before the FDA’s deadline.
What is traceability?
The FDA describes traceability as “the ability to follow the movement of a food product and its ingredients through all steps in the [food] supply chain, both backward and forward. Traceability involves documenting and linking the production, processing, and distribution chain of food products and ingredients.”
According to the FDA, “in the case of a foodborne illness outbreak or contamination event, efficient product tracing helps government agencies and those who produce and sell food to rapidly find the source of the product and where contamination may have occurred. This enables faster removal of the affected product from the marketplace, reducing incidences of foodborne illnesses.”
The FDA states that these new traceability requirements “will allow for faster identification and rapid removal of potentially contaminated food from the market, resulting in fewer foodborne illnesses and/or deaths.”
48 million sick people per year
According to estimates from the Centers for Disease Control, an estimated 48 million people get sick, 128,000 are hospitalized, and 3,000 die from foodborne diseases each year in the United States.
Passed in 2011, the Food Safety Modernization Act gave the FDA more authority to oversee and enforce supply chains and take a preventative rather than reactive approach to foodborne illness. FSMA applies to all foods regulated by the FDA, representing about 75% of the U.S. food supply, according to NIST.
Consumer Goods wrote that because recalls are so expensive and inefficient, “food and beverage companies will benefit from the greater precision and transparency,” that will result from the guidelines.
Consumer Goods added that food manufacturing companies must start taking steps now to ensure compliance by the January 2026 deadline.
“The first step is assessing current capabilities, looking at all impacted products, business units and the technologies utilized. The fact is traceability is not just a compliance issue. Traceability impacts functions throughout an organization, including HR, finance, sustainability, manufacturing, safety and quality, technology systems, distribution, cybersecurity, and consumers."
To learn more about traceability and its importance for food manufacturing companies, join us on April 3rd at 12pm CST for a special webinar featuring Joel Chappelle, Attorney and Consultant at Food Industry Counsel LLC. Details here:
Contributors
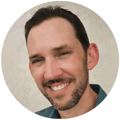
Ben Hartman
From HACCP certification to the basics of hygiene, our on-demand courseware has you covered.
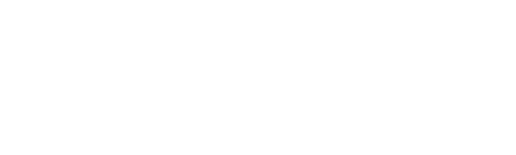