
Author: Ben Hartman | July 9, 2025 | 4 Min Read
Risk Management and Damage Control - Why You Should Get Started Today on Your Next Mock Recall
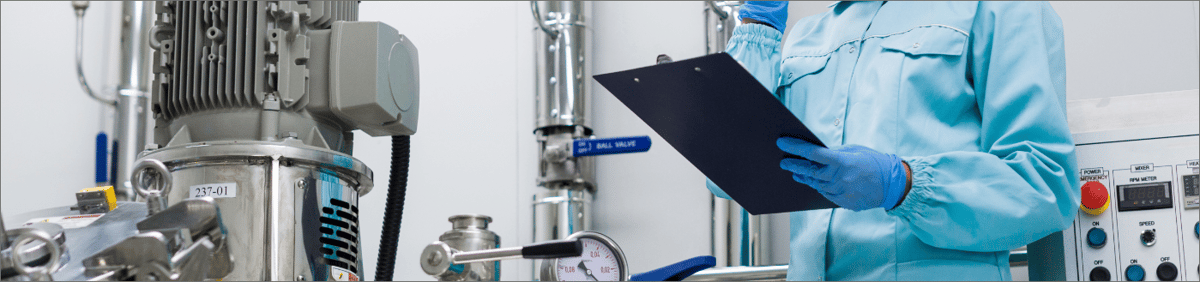
Over a single one-month span this summer, the U.S. Food and Drug Administration reported 20 food safety recalls.
With reasons ranging from undeclared allergens to Salmonella, Listeria, and elevated levels of copper, the recalls give a glimpse of the wide range of food safety hazards that can trigger a recall and jeopardize the future of a food industry company.
According to figures from a joint industry study by the Food Marketing Institute and the Grocery Manufacturers Association, the average cost of a food safety recall is $10 million. And that figure is in addition to the often devastating impact on a company’s public reputation.
But the damage caused by a recall is directly linked to the recall response carried out by the company in question, and how quickly and directly it can mobilize to mitigate the fallout of the recall.
The FDA states that mock recalls are a key way to prepare a facility for the event that they need to carry out a voluntary recall.
“A firm that anticipates complex recalls may want to consider additional preparatory steps, such as mock recalls, to verify the firm’s recall readiness. Mock recalls familiarize personnel with the recall process and may improve the effectiveness of the firm’s recall program.”
One of the main ways to boost a company’s recall readiness is to carry out mock recalls.
What is a mock recall?
A mock recall is exactly what the name implies - it is a simulated product recall exercise in which a company takes one of its products and practices tracing the ingredients that need to be recalled and removing them from the market. A mock recall is meant to test a company’s readiness for a recall and to practice better damage control if and when the moment of truth comes.
Mock recalls are essential for developing a proactive approach to food safety and recall management.
In a recent interview with Rootwurks, Andrea N. Griffiths, Retail and Supplier Audit Program Manager at ASI, broke down what it takes to carry out a mock recall and why they are so important for the safety culture and recall management plans of food industry companies.
What is the point of a mock recall?
According to Griffith, there are four main reasons to carry out mock recalls:
- To protect your brand
- To test the gaps in your processes and systems
- To prepare for actual emergencies
- To practice and expedite your processes
“You want to make sure that your trace is good, that you can trace one step forward and one step back in your processes. This prepares you for a real recall event and lets you know what you need to do,” Griffith said.
She added, “it’s also a way to show that you’re following regulatory demands and adhering to compliance,” specifically the regulatory requirement for an effective recall plan.
Carrying out a mock recall also helps find gaps and weaknesses among team members.
“Mock recalls help bridge gaps in your systems and help you train cross-functional teams that aren’t always working together.”
Is recordkeeping important?
Performing a mock recall is impossible without detailed records to trace the steps in your manufacturing process.
“Your recordkeeping is the most important aspect. You can’t do a mock recall without the documentation and details on what you have coming in,” Griffith said, adding, “if you don’t have documents, you have nothing. You lose all your traceability.”
Good recordkeeping is essential because you have to know where all of your ingredients are coming from, and how much has already gone out and to where.
“In a mock recall, 98 to 100% of the product should be pulled back. You check how much of the product went out, and that will tell you how much you should be able to account for at your facility.”
What are the first steps in carrying out a mock recall?
While mock recalls may seem complicated and difficult, Griffith noted that it doesn’t cost any money to get started and “though it looks complex, it doesn’t take long to learn and you get it under control pretty quickly.”
Griffith said that when performing a mock recall, you should first test out your most difficult-to-trace ingredients.
“You want to check your inventory and know what you have coming in, and adding lot numbers or an identification code, and then create a system that tracks it all the way through from the receiver-storage process and holding.”
Griffith said that she recommends companies perform mock recalls twice a year, and that they should require around 4 hours.
“It’s daunting, but it's very doable. Just start today, and eventually you’ll look back and say we got this. But you gotta start right away,” Griffith said.
Contributors
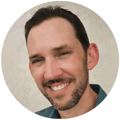
Ben Hartman
From HACCP certification to the basics of hygiene, our on-demand courseware has you covered.
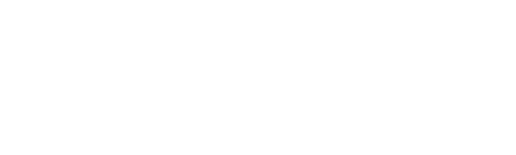